Diary of a Building: REDELCO HOUSE
Early in 2003, Larry Scarpa, a principal of the award-winning architectural firm Pugh + Scarpa Architects, contacted me and explained that he had a client who was interested in building a five-thousand-square-foot concrete, steel, and glass house in the Hollywood Hills. The site was remarkable, With dramatic views of the San Fernando Valley and San Gabriel Mountains. At the same time, however, like so many hillsides in Los Angeles, it was a difficult parcel to build on because of a very steep grade with limited access and no staging or parking areas.
The client, a successful entrepreneur and fitness enthusiast, wanted a house that was “spatially open and quintessentially Californian” in the modernist sense of Richard Neutra’s Lovell Health House. And, in addition to a sunken living room, study, and master and guest bedrooms, he requested amenities such as a two-story interior space and bridge, an infinity-edge pool, a Jacuzzi, a large steam room and whirlpool, a gym, and oversize sliding glass doors that would open the house up to the outdoors.
When working with Scarpa, the project budget and final cost are developed at the beginning of the design process. Several contractors were interviewed and asked to present outlines of their fee structures as well as a strategy for building within the framework of a guaranteed price for the entire job—with no extras. After reviewing the proposals, they selected RJC Builders. Having worked with Pugh + Scarpa on several other jobs, we had developed a collaborative relationship that was very productive. They also noted that we possessed the skill, motivation, and enthusiasm that are necessary for a job that has the challenges this one had.
As a builder, I am always interested in the client’s and architect’s specific focus and concerns. Beyond the standards of quality, cost and schedule that form the core values of our company, each party brings its own particular desires and focus that we take very seriously. An established businessman, the client expressed an interest in being involved with and aware of all the financial transactions, as well as a financial approach that he could be comfortable with. To this end, we proposed a guaranteed maximum cost and a competitive fee structure. We expanded our spreadsheets and included copies of all invoices and receipts with each monthly billing and kept him apprised of any ongoing negotiations.
On the architectural side, whenever possible, it’s our preference to work with the architects throughout the design development and construction document phases, making recommendations on constructability and valueengineering elements of the design as it evolves, and is required. This is important not only because it lessens the questions once construction begins, but also because it enables us to achieve our goal of setting a fixed cost for the project and a ready-to-start date the day the architect acquires the building permit. Too often I’ve been invited to bid on projects at the conclusion of the design process and permitting phase and have seen bidders be over budget by as much as fifty percent. It’s unfortunate and can have a disastrous effect on whether or not the building is built.
Ching Luk, the project architect in Scarpa’s office for the residence, worked tirelessly drawing, detailing, firing off questions, redrawing, coordinating with consultants, and integrating information to produce the working drawings. The result was a set of construction documents that numbered over a hundred sheets, the largest I have ever seen for a residence. The time invested on these drawings makes the builder’s job that much easier. Not only are the number of questions in the field greatly reduced, but we’re better able to guarantee prices for the many components of the project, from concrete finishes on foundation work to custom door ocks designed by the architect. This can-and-will-do attitude on the part of my staff and the staff at Pugh + Scarpa was a daily part of the construction process that I will attempt to discuss in the accompanying “Diary.” Although other contractors could have completed the job satisfactorily, I’d like to think that we were active participants in a process that produced something very special.
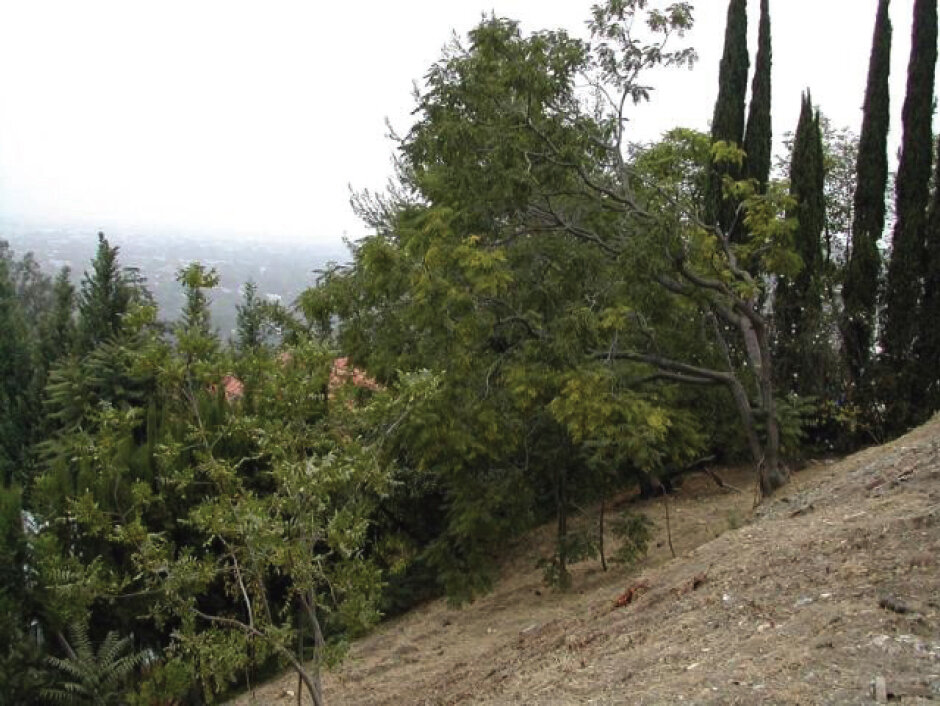
08.03.02
The hillside was considered too difficult to build. A combination of factors— the steep grade, limited access, absence of parking and no flat spot to store materials or stage supplies on—kept the land vacant. But the view toward the north made the project compelling. Large expanses of glass could be installed without worrying about direct sunlight or the need for shade.
08.26.02
The steep site became a kind of litmus test for subcontractors. RJC established early on that we would not pay a premium because of the site’s challenges. We located several other construction projects nearby to take our grading soils, and others to import their soils when it came time to back-fill the basement walls. Grading after the basement excavation involved heavy digging equipment perched upslope on a tight ridge.
Access was a constant issue. The small lot and uphill location left little room to maneuver. The earthen ramp was installed and altered throughout the foundation phase, depending on the equipment needed. We outlined our approach prior to the bidding so that the ramp work was a fixed cost for our grader and never an issue when modifying or relocating it was required.
We have completed many projects with our soils engineer, Grover-Hollingsworth & Associates, Inc., and have established a productive working relationship based on the mutual understanding that we are both interested in providing the highest quality work. Every site has unique soils that require unique solutions. This particular site contains a high quantity of shale, which, while good for drilling and excavating, is porous. Water seeps right through and begins to attack foundations. This means that the basement waterproofing is of primary importance, and the perimeter drainage systems at the foundation and retaining walls will be like little streams. To accommodate the flow, we doubled the basement wall waterproofing and increased the diameter of perimeter drains from four to six inches.
08.30.02
On each job there seem to be two or three subcontractors that shine and become the project All-Stars. On this project I would have to put Rebar-Ranch from Santa Paula at the top of the list. The owner, Jay Guertin, hand-built this rig from a discarded Bobcat tractor chassis specifically for tight-access hillside foundation work. It is so small that it must be operated by remote control. Despite being skinny, this rig can drill to twenty-five feet on a slope up to a forty-five degree angle. Aside from his MacGyver-like ingenuity, Guertin’s optimistic attitude is a prerequisite to digging hillside foundations. He’s drilling a three-foot-diameter by twenty-foot-deep caisson.
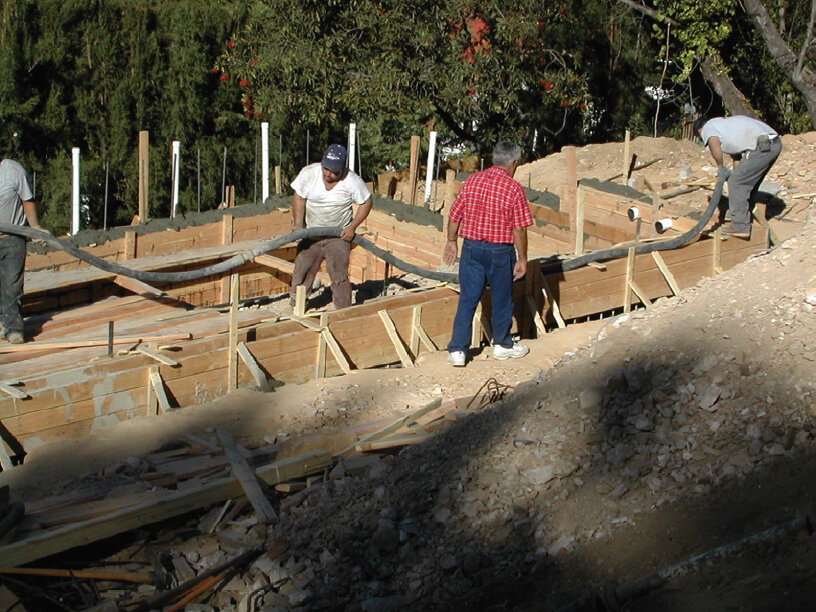
12.02.02
To the architect’s credit, the builders for his custom homes are brought in early. Using his design parameters, we initiate discussions of constructability, cost, and schedule. We discuss the foundation system at the outset, during the schematic design phase. A hybrid caisson/grade beam system turned out to be an efficient and cost-effective solution since the soil was quite stable with little heavy rock. We were able to use a foundation system without oversize caissons or excessive grade beams and cumbersome structural slabs.
We were able to “claim” a patch of flat landscape on the steep site by adding a retaining wall on the downslope edge of the property. The client had to weigh the cost of the retaining walls against the value of level land on this property. We also priced the work if done at a later date, after the house was complete. It turned out to be an easy decision; the level ground also gave us a staging area (albeit a small one) on the north side of the building.
Phasing the project’s various elements usually comes down to budget and schedule. More often than not, we prefer to leave pools, spas, and water elements out until we are well into the project. On Redelco, however, we decided to incorporate the pool and spa into thefoundation work. We made this choice not only because of limited site access, but also because we received better pricing by grouping all of our caisson work together.
12.17.02
Again, we must remain agile when challenges present themselves. This is not the preferred equipment for setting steel columns. However, for structural reasons, the steel columns had to be deeply embedded into the caissons and long periods of crane time were needed to hold columns in place while the temporary shoring was installed. The “Grade-All” forklift gave us both easier access and a much lower hourly rate than a conventional crane setup.
Some of the more satisfying moments of the project occur when we start to recognize the architect’s vision in spatial terms. Although the column is temporarily shored up, awaiting the concrete pour, we begin to see how Scarpa has framed the living room view. The building begins to claim the site.
01.13.03
Something that’s often overlooked in concrete work is the skilled carpentry. The quality of carpentry for the foundations easily matched the carpentry for the framing of the building. The concrete formwork is hard enough, but is a genuine test when there are few benchmarks to work from. Often we are working from a surveyor’s point a hundred feet away. All of our north-south foundations had multiple steps with grade.
All of the rebar for this job was cut and fabricated in the field due to the lack of staging areas and restricted site access.
As the concrete slab formwork and rebar is set for the cantilevered floor we get new perspectives on the site. We have more than three times the weight in rebar steel than we do in the steel columns and beams.

05.26.03
A bed of clean three-quarter-inch gravel laid against the basement wall allows any subterranean water to flow through a vertical drainage board into subterranean drains, and then quickly off-site.
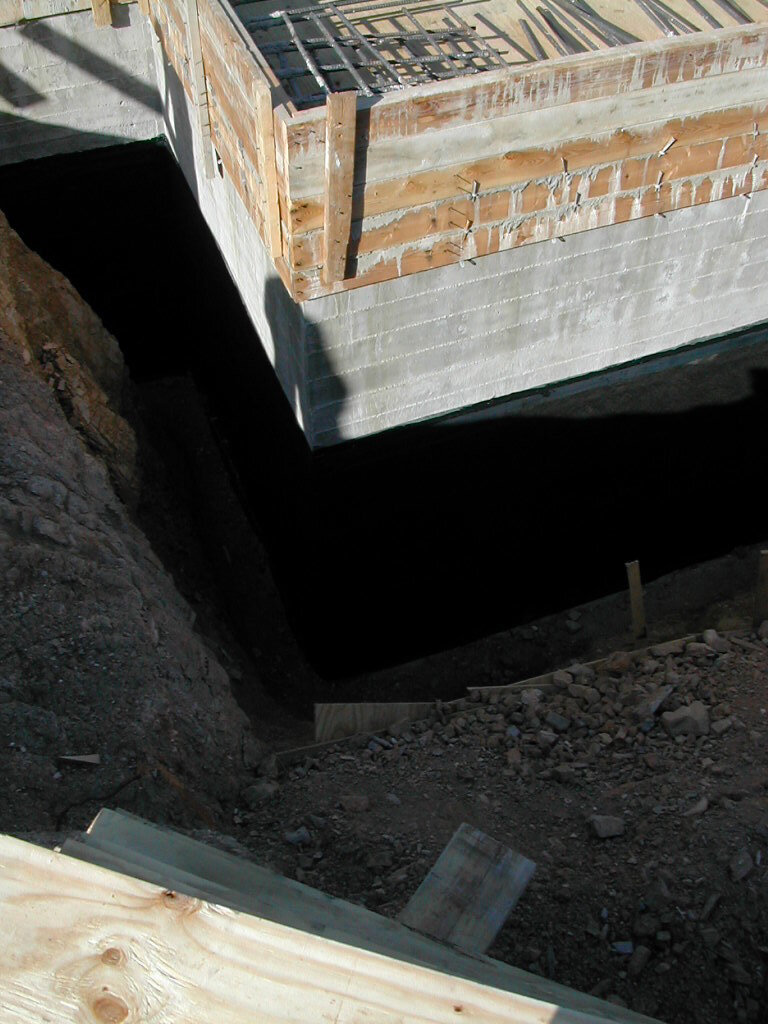
Working with exposed concrete is one of the more challenging tasks a builder faces. The foundation carpentry work goes from merely holding and forming the cement while it cures, to a high-profile finish that emerges from the basement to become the exterior shell of the building. At this point, the location of every board and support brace is key to attaining the design result we desire. Working with Scarpa on previous projects proved invaluable here, since we understand his vocabulary and have a sense of what is important to him. We are constantly trying to put the effort and money where you’ll see it, and where it matters most.
03.11.03
Modern residential architecture often involves the introduction of commercial and industrial building techniques. We strive to be at the cutting edge of these technologies, using various systems and techniques in innovative ways when appropriate. Whether door and window, heating and air-conditioning, structural systems, or hardware, the architect’s choices should not necessarily be limited to “residential” products and technologies. We are using a concrete shoring system designed for parking garages to form the sunken concrete living room floor above.
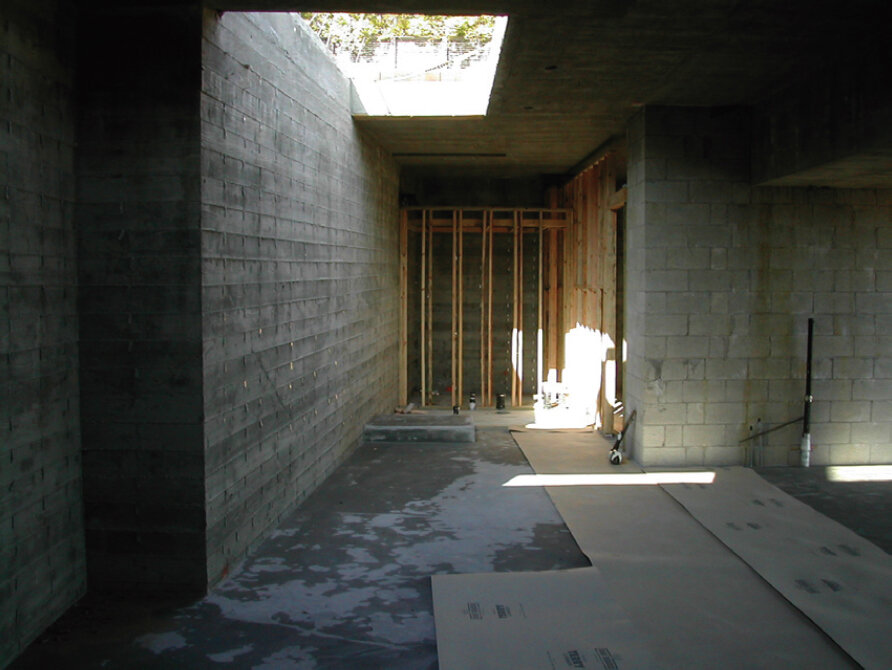
05.22.03
As the basement concrete formwork is removed, once again, Scarpa’s intentions are revealed and new opportunities arise. The opening in the basement ceiling for the stair is also considered a light well and will influence the design of the staircase. The handrails and treads are revised to be made more porous, allowin for additional direct and indirect light to filter into the basement. One of our goals is to provide an open atmosphere for the architect’s creative process throughout the building process. As long as we are watching the budget and schedule, I find it critical to the success of a design to allow design latitude during the construction process.
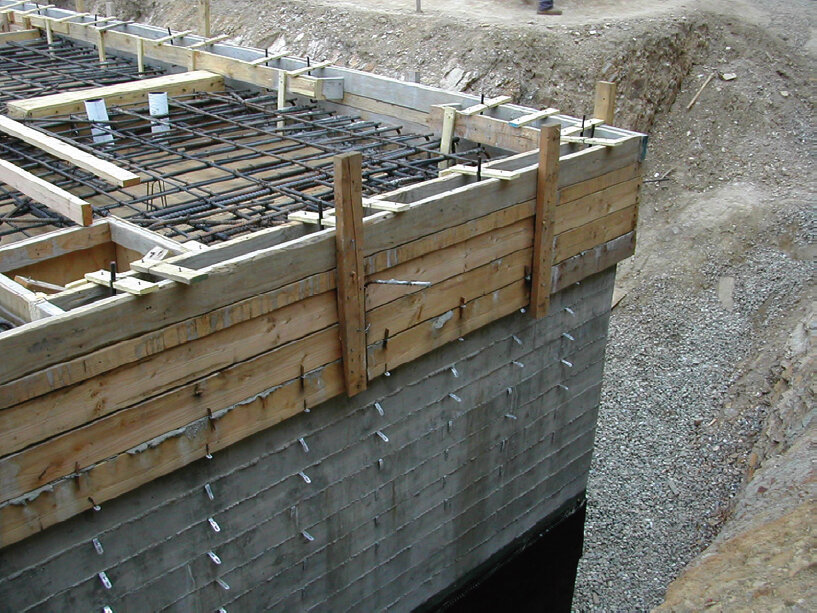
Finely crafted architecture is often revealed in how well similar or different materials are joined together. Unlike traditional architecture, which uses the convenience of “trim” (casement, baseboard, or crown molding) to hide the joints between elements and materials, modern architecture exposes itself in a reductive manner. This seemingly simple slab-meets-wall detail is more than meets the eye. We must align the new formwork pattern with the existing pattern of the wall. Not difficult or obvious, unless we miss it.
08.07.03
Few things are as gratifying as seeing the building grow on the site. Again, we begin to see the intent for the second floor come to light, and this will influence everything from window location to furniture layout, which in turn will impact electrical and lighting decisions.
From the second floor, views of the valley and mountains as well as sight lines within the house begin to emerge. The photo was taken looking from the master bedroom to the living room below.
A steel beam sitting on the second story floor, awaiting installation. Generally, I am not inclined to run a job sequentially by completing one phase and then moving to the next. Although some subcontractors disagree with this view, I find it more productive to merge phases and work concurrently. We will often have concrete, steel, and wood framing subcontractors running side by side for weeks. A not-so-subtle request of our steel installer at this moment was to have the wood framer slow down. The start of a job somehow never has the same urgency as the last few frenzied weeks.
08.10.03
Although the building envelope is designed, and we’re not expecting any major revisions, our weekly meetings are vital during the framing stages. Now we can easily raise or lower windows and adjust or even relocate partitions to make subtle changes and refinements to the interior spatial experience.
Regardless of the size of the project, material waste and run-off is a constant concern when constructing a building. Our oceans often bear the brunt of sloppy construction practices such as slurry from concrete and painting cleanup. RJC Builders observes sustainable practices in building. We maintain a diligent “Storm Water Prevention Plan” that is stricter than required by our local agencies. Consistent sandbagging and monitoring of the perimeter is one aspect of the plan.
Upon seeing the light strike the concrete wall (just to the left of the ladder), Scarpa had the idea of placing ten small colored glass cylinders in the wall, to allow light to pass through.
On my weekly job site walk-throughs, I touch on three primary aspects of the project: quality, cost, and schedule. As we move from room to room the question in my mind is: “What could we be working on here that we’re not?” The minute the steel frame is installed, I want to see the tracks for the oversize glass doors that fill these bays. In reality, we have been working off-site on these tracks and doors for months in anticipation of this setup. Our progress on any given day is dictated by our planning efforts weeks, sometimes months, prior to installation.
09.15.03
Raking light against a board-formed concrete wall; the building begins to find its voice as some of the final pieces emerge from the seeming disarray of construction. Sometimes on a site I feel like the first person to read a great poem. The shadow of the cast-in-place concrete beam above provides shade for the front entrance door just to the left of the steel column.
10.02.03
There were no structural drawings for this cantilevered shelf, which will eventually hold a sink and a barbecue. After pouring nearly seven hundred cubic yards of concrete for the foundations and walls, our subcontractor didn’t even need to ask.
As the interior partitions begin to go up, we’re not afraid to let some of the non-structural wall articulation lag slightly behind. The two by six projections here start to outline the alcove for the flat-screen TV, for which we have not yet received exact specifications. By installing enough framing to give the architect a physical idea of the object, he can alter it in the field without the additional cost of removing and replacing completed work.
TGIs, PARA LAMs, OSB, and CDX Stuct 1—this alphabet soup of wood-framing members and sheathing is growing as building codes become stricter and stricter each year, especially as it pertains to seismic strength requirements. As cumbersome as building codes and the permitting process can be, we get safer and more substantial buildings because of them.
The cantilevered beam in this wall meant GK Plumbing had to run the vent line along a circuitous route around the beam and posts, but we didn’t hear a single complaint.
I gained great respect for the working relationship between the structural engineer and the architect on this project. The engineer, Gordon Polon, and Scarpa not only solved the structural requirements in an elegant manner with slender, well-spaced steel columns set back from exterior enclosures, but they did it while making three separate buildings that sit within inches of each other. The main house is split into two volumes, separated by glass walls and skylights. The third structure is lifted twelve feet off the ground and connected by a lightweight perforated-steel bridge. Here, we see the three roofs with their narrow slots of separation.
Not a bad place to go to work. The roof diaphragm plywood installation is complete and waiting for a city inspector prior to roofing. A box of shear nails is left behind as confirmation for the inspector that we have used nails that are the proper length and thickness.The easier we make his job, the easier he’ll make ours. The roof required seventy-six sheets of plywood with one hundred and twenty-eight nails each. That is almost ten thousand nails.
Experimentation makes it all worthwhile. I can’t imagine a project where all the details, let alone form and space, are the same as the last one. This is one of the pleasures of working on custom-built houses. Scarpa generally starts with a clear idea of what he wants but is open to how we technically solve the details of fabrication and installation. The location of the copper cladding for the exterior skin of the building was established early, along with a price-per- square-foot cost. Through samples such as this one, we refined the proper proportions, joint sizes and connection details. The underlayment of a Grace Ice/Water Shield was also resolved; should water infiltrate a seam, we have a second layer of weather protection for the wood framing behind the copper cladding.
It seems difficult to compete with the simple economics of prefabricated fireplaces unless you have a memory of the real thing. In calculating the budget, we earmarked the funds for a brick and concrete fireplace, but as we progressed through foundation and framing the money was eyed as a possible line item cut. Fortunately, it survived and became a centerpiece of the living room. Scarpa had forms milled from dense foam on a CNC machine. Installed, the cast concrete fireplace mantle and surround give the appearance of a billowing curtain across the open hearth.
As we enter the last phase of construction, it becomes clear that the client has not been editing his options list. The budget was tight to begin with and we pushed it all the way to the end. As a means to helping get us back on budget, we locate some unique tile at a terrific savings and acquire the exterior stone directly from Mexico. I introduce the tile subcontractor to Andujar & Son Tile Co. and allow the client to pay them directly, giving him my wholesale cost without my fee while passing along the savings on material. Milton Andujar (the “& Son”) thoughtfully coordinates his work shirt with our choice of tile.
12.28.03
I am forever cognizant that our efforts, at bottom, are geared to providing shelter. Translation: Everything must be flashed to keep water out. At Redelco, Scarpa elevated a utilitarian part of the project and combined several items into an elegant and innovative architectural detail. The long flat portion provides the terminal point for the built-up roofing, while the square channel-shaped piece in the center is a scupper giving rainwater a low point to exit the roof.
Modern architecture doesn’t always leave much space for mechanical chases, that is, a place to put all of the ducts, pipes, and cables. Here, we were given the upper corner of a garage ceiling and it is immediately jammed with heating and air conditioning ducts, gas lines, high voltage wiring, fire sprinkler lines, hot and cold water, security, telephone, cable TV, computer, and AV lines. We added a storage cabinet the same depth as the chase so that the chase was continuous with the cabinet face and not a visual blight. Although not required structurally, we clad the interior garage walls with plywood, making installation of storage shelves or racks simple and flexible.
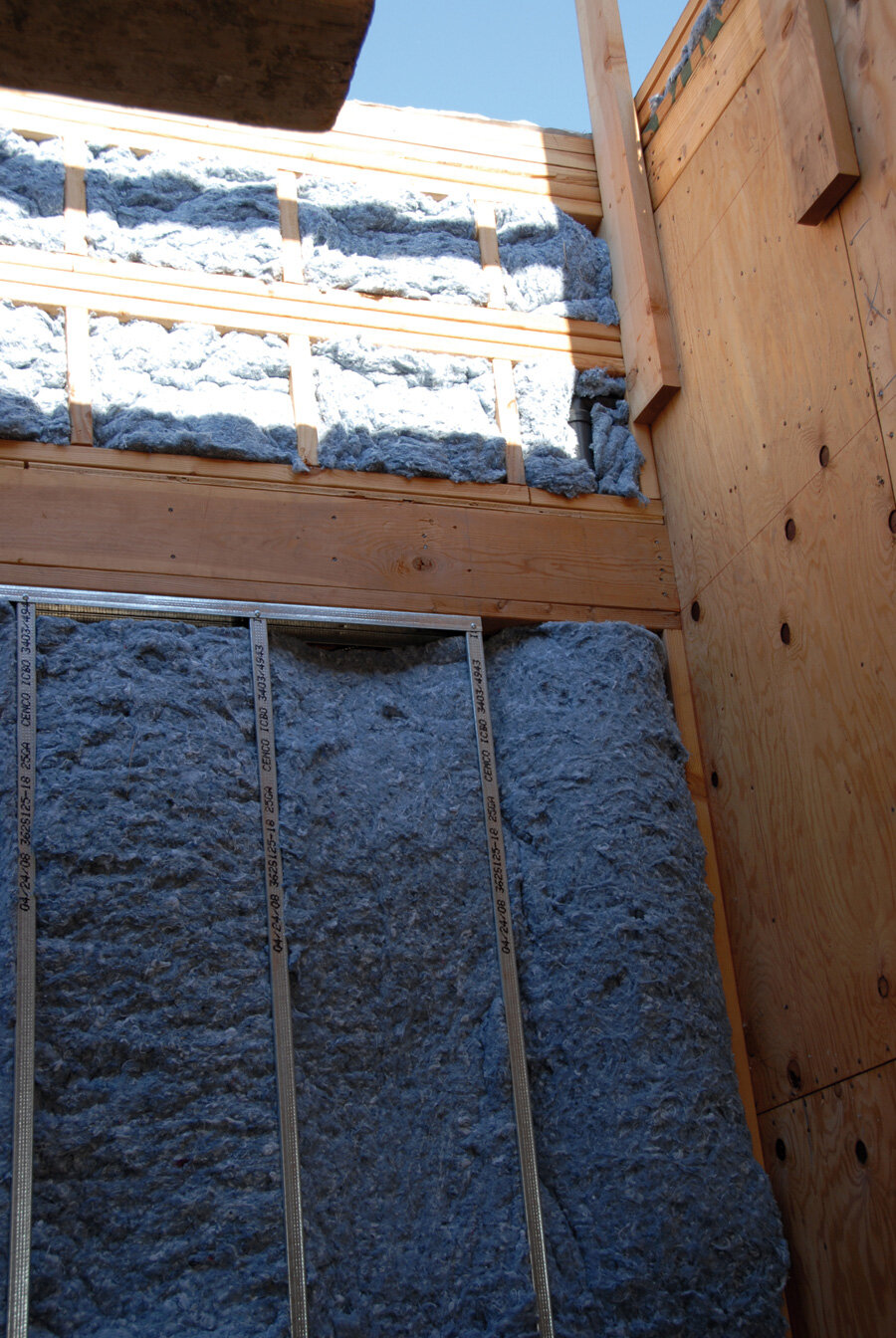
01.02.04
Many interesting innovations are taking place with building materials these days. Materials are being reformulated and reverting back to simpler base ingredients. Example: Fiberglass batt insulation, while still the industry standard due to cost, is gradually being replaced by an old favorite—recycled cotton jeans. “R-30 Unfaced Ultra Touch Cotton Batts” are chemical-free and environmentally safe both in terms of manufacturing and recycling. Also, workers are not exposed to dangerous airborne fiberglass strands during installation.
02.18.04
After the drywall sheets have been installed inside or the paper and lath installed on the exterior, the most critical aspect of the finishes begins, placement of the bent or extruded metal shapes used to establish all corners, joints, changes in plane, and terminations. The installation of these metals brings the rough framing, which can vary a quarter inch over ten feet, into perfect plumb and straight line. The work takes a combination of talent and great patience.
A standard drywall installation doesn’t require the application of a continuous topping, or skim coat. However, we provide a final skim coat over all interior drywall surfaces. The skim coat creates a museum-quality wall and assures that no seams or fastener dimples will telegraph in the future. The skim-coated wall is subtly different than naked drywall. The wall, while perfectly flat, will have the slightest undulation and, I think, a greater sense of weight or mass.
The various trades working concurrently on flooring tile, the swimming pool, exterior copper cladding, finishing the drywall skim coats, painting, cabinets, fireplace flue, and handrails. The rollers for the large doors can be seen in the track where the living room ceiling edge meets the sky; these doors have been rough fit and are out being fine-tuned prior to installing the glass.
A critical topic at our weekly job meetings is scheduling. We start with a detailed timeline for the entire project, and then each week our superintendent updates a three-week schedule, which immediately allows us to see where we’re at in terms of the overall schedule. Quality takes time, so I don’t make promises about completing work early, but we always expect to run on schedule. When we get to the final stage of the project, scheduling questions are always more pressing. As a client begins to see the finished product for the first time, their enthusiasm becomes palpable. They want to move in now! Unfortunately, it’s my duty to remind them that the last ten percent is half the job.
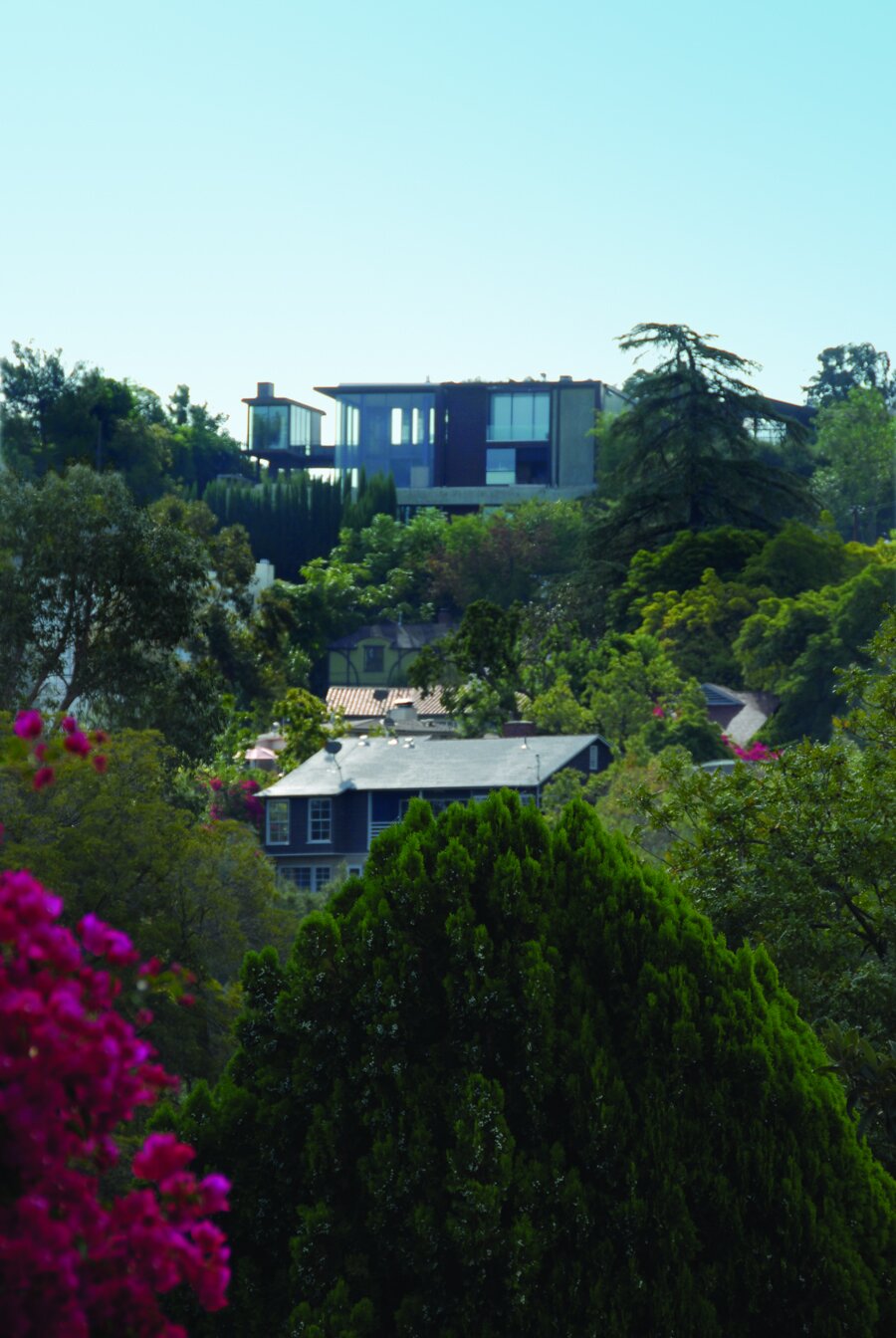
“...so shines a good deed in a weary world...”